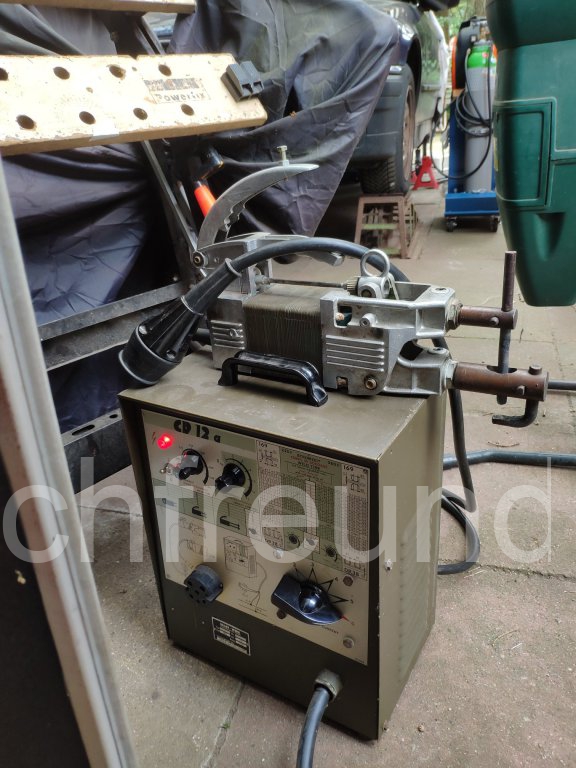
Nach einem Tag, an dem das schlechte Wetter die Weiterarbeit verhinderte, wurde nun die Schweißnaht des Außenradlaufs verschliffen. Dabei kamen der Winkelschleifer mit der Schruppscheibe, der Proxxon-Schleifer mit einer kleinen Schruppscheibe, der Winkelschleifer mit einer Fächerscheibe und ein kleiner Druckluft-Tellerschleifer zum Einsatz.
Die Naht sieht gut aus und die Bleche passen gut. Da dürfte wohl nur wenig Spachtel fehlen, um die Oberfläche zu glätten.
Es fehlt jetzt noch die Verbindung zwischen den Innen- und dem Außenradlauf. Um die Position der Schweißpunkte festzulegen wird mit einer Schiebelehre gemessen, um die Position des Innenradlaufes zu anzuzeichnen. Die Schweißpunkte werden dann mittig angezeichnet.
Die ersten beiden Schweißpunke wurden mit dem Schutzgasgerät gesetzt. Dazu wurde der angezeichnete Punkt an gekörnt und mit einem Schweißpunktbohrer bis auf das untere Blech gebohrt. Durch dieses Loch wurden dann beide Bleche miteinander verschweißt und das Bohrloch geschlossen.
Das funktioniert sehr gut, ist aber relativ aufwändig und bedeutet auch viel über Kopf schweißen und schleifen.
Zum Glück steht ein altes Punktschweißgerät zu Verfügung und auch der passende Radlaufsatz ist vorhanden. Nach ein paar Probeschweißungen an Blechresten kann es losgehen. Einziges Problem, die Kabel reichen gerade so bis zur Schweißstelle. Es bedarf also einigen Verrenkungen, um die Schweißpunkte an allen Stellen zu setzen.
Trotzdem geht es wesentlich schneller als mit der Schutzgasmethode. Die Bleche sind für das Punktschweißen vorbereitet. Nur die Oberkante am Innenradlauf musste noch mit Schleifpapier angeschliffen werden, damit die Punktschweißzange elektrischen Kontakt hat.
Trotz einiger Pausen wurde die ungekühlte Schweißzange nach einigen Schweißungen sehr warm. Lederhandschuhe waren Pflicht. Die Schweißpunkte sehen fast so aus, wie ab Werk.
Die geschliffene Naht hatte noch ein paar kleine Stellen ohne Schweißpunkt, diese Stellen wurden kurzerhand nachgeschweißt.
Und auch im Radkasten gibt es noch ein paar Rostlöcher, rund um eine Schraube herum. Dies ist die gleiche Schwachstelle, die schon auf der rechten Seite geschweißt werden musste.
Mit Malertape und Filament-Klebebad wurde wieder die Größe und Form der Reparaturstelle und die Position des Schraubgewindes festgehalten. Auf der Innenseite wurden Linien gezogen, um die Position des Schraubgewindes festzuhalten.
Das Reparaturblech sieht einfach aus, ist aber in zwei Richtungen gekrümmt. Vom Innenradlauf ist noch Blechverschnitt übrig. An diesem findet sich ein passender Blechbereich, der nur noch minimal nachgearbeitet werden muss.
Das Blech wird angepasst und mit Magneten angesetzt. Die Position des Schraubgewindes wird über die angezeichneten Linien auf dem Radkasten auf das Reparaturblech übertragen.
Der Schweißbereich wird wie zuvor angeschliffen und gereinigt. Dann wurde das Blech mit ein paar Punkten angesetzt. Dann war erstmal Feierabend.