Das Seitenteil ist die aktuelle Herausforderung. Es sieht einfach aus, hat es aber in sich.
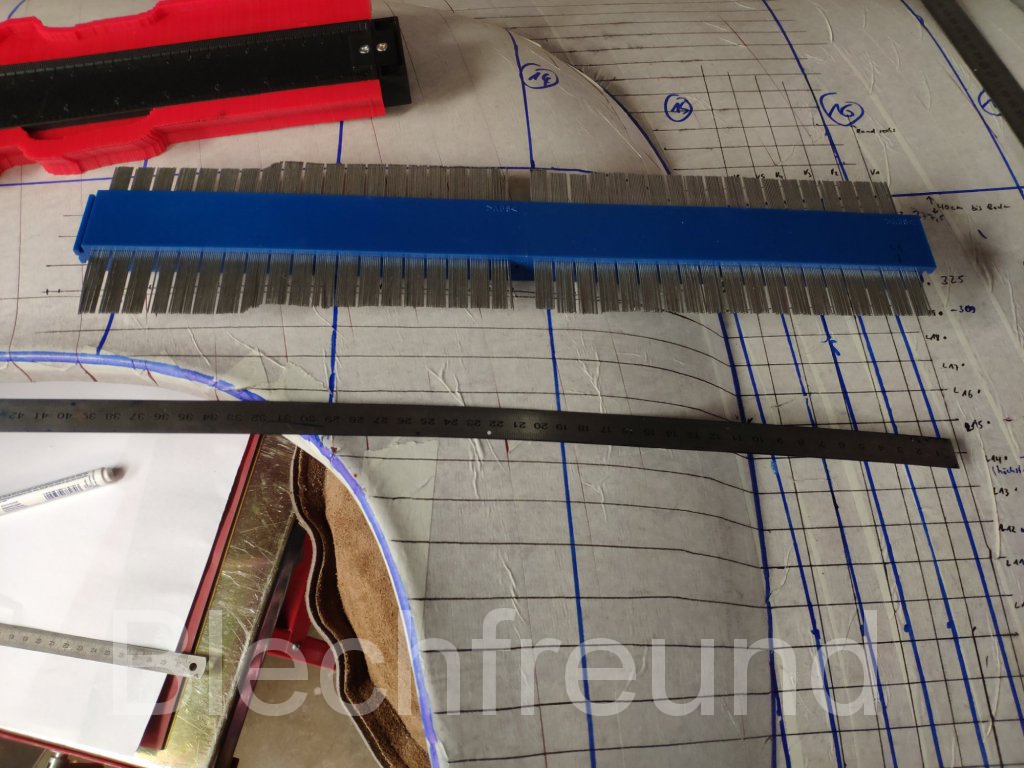
In mehrere Richtungen gewölbte und gekrümmte Flächen garniert mit einer gekrümmten und gewölbten Sicke und das Ganze natürlich unsymetrisch. Dazu garniert mit einem Radlauf der sich in Form und Verlauf verändert und einer abgerundeten Abkantung an der Unterseite.
Die Form ist so komplex, dass schon die Vermessung zu Herausforderung wird. Aber schauen wir ersteinmal auf die geplante Vorgehensweise.
Der Fokus liegt nun auf dem schwierigsten Teil. Der Plan ist, die Form in den Rechner zu bekommen, um eine Form zum Blechpressen, oder zumindest eine Klopfform zu bekommen, die dann auch gleich passend für die Fahrerseite ist.
Die Form soll auf Papier übertragen werden und dann in den Rechner kommen, wo mit Software ein Modell daraus erstellt wird. Das Einfachste wäre ein 3D-Laser-Scanner. Die sind jedoch noch unerschwinglich.
Also der klassische Weg. Auf den relevanten Bereich wird ein Raster gezeichnet. Der Linienabstand ist ca. 17 mm. Die modernen Profilschablonen sind zwar schön, aber die Messtiefe mit 3 cm viel zu gering. Glücklicherweise habe ich vor Jahren mal Schablonen von Lidl (PowerFix) gekauft, die zwar nicht so haltbar sind, aber dafür eine hohe Nutztiefe haben.
Profillinie für Profillinie wurden abgenommen und auf Papier übertragen. In Längsrichtung 23 plus 2 zusätzliche für die Unterkante. In der Senkrechten wurden 7 Linien (nun mit dem passenden modernen Profilmesser) übertragen. Zusätzlich die hintere Radlaufkante und in 45 Grad Neigung die gebogene senkrechte Sicke zum angedeuteten Kotflügel. Also mehr als 150 Kreuzungs-/Messpunkte sind so definiert.
Die Schablonen kamen danach auf den Scanner. Alle die länger als 30 cm waren, wurden in zwei Teilen gescannt und im Rechner wieder zusammengeschnitten.
Der nächste Schritt ist es, die Schablonen in FreeCAD nachzuzeichnen und ein 3D-Model daraus zu bauen.