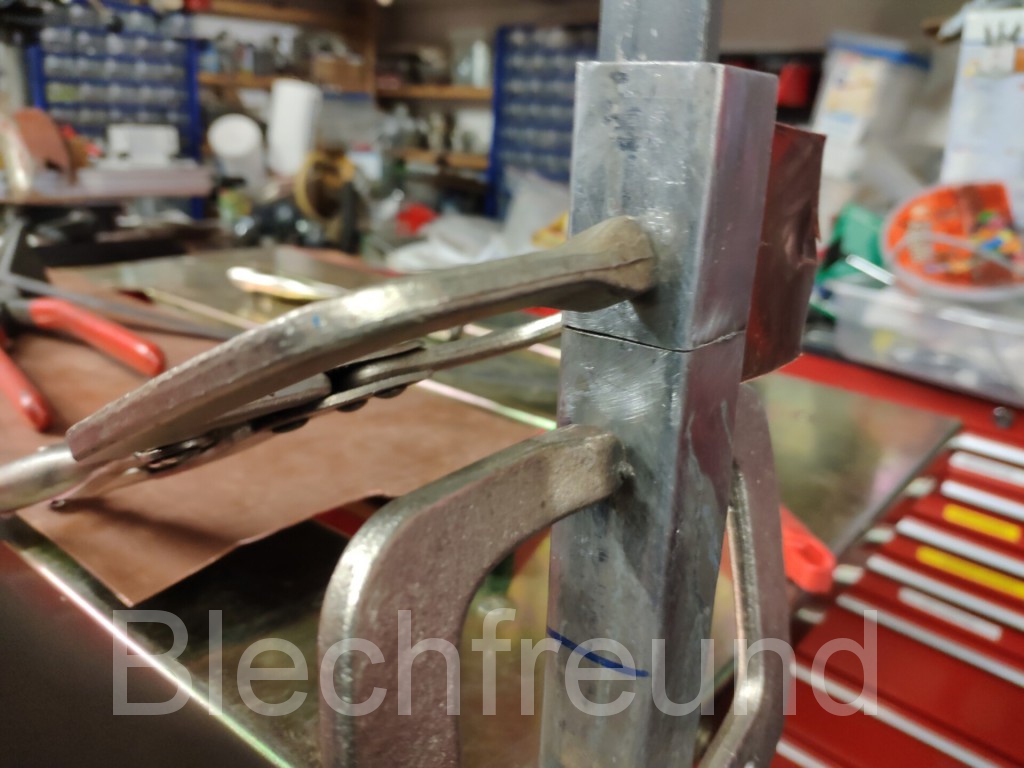
Karosseriebleche auf Stoß schweißen ist der Traum jedes Hobbyschraubers. Als Universalgerät landen die meisten beim Schutzgasschweißgerät. Das ist auch für fast alles zu gebrauchen, aber beim Karosserieblech würde ich wohl, wenn stumpf geschweißt werden soll und Zeit keine Rolle spielt, nur noch zum WIG-Schweißgerät greifen.
Das Schweißgerät Stahlwerk AC/DC WIG 200 Puls ST IGBT habe ich hier ja schon mal vorgestellt. Beim Schweißen des Radkastens waren einige Zentimeter zum Üben vorhanden. Da war das eine der beiden zu verbindenden Bleche allerdings 1,2 mm stark.
Der Radkasten konnte auch bequem auf dem Schweißtisch platziert werden, sodass der Schweißbereich immer horizontal lag. Also quasi Idealbedingungen für das Schweißen.
Bei der C-Säule ist es nun anders, diese ist fest am Auto verbaut und muss in dieser Position auch geschweißt werden.
Außerdem ist die Blechstärke mit 1mm dünner und die Wärmeableitung schlechter. Mit anderen Worten, das Blech kann schneller durchbrennen und die Gefahr durch Wärme Verformungen in das Blech zu bekommen sind größer.
Das abgekantete Reparaturstück ist deutlich länger als zur Reparatur erforderlich. Dies hat zwei Gründe. Erstens kann man sich die besser passende Seite aussuchen, obwohl die eigentlich gleich sein sollten. Zweitens kann ich ein Stück vom Reparaturstück abtrennen und dieses zum Üben wieder anschweißen.
Da es sich hier um einen später sichtbaren Bereich mit geraden Kanten und Flächen handelt, stechen Fehler hier später leicht ins Auge.
Als Erstes werden die zu schweißenden Bereiche gereinigt. Falls das Blech fast blank ist funktionieren Roloc Schleifscheiben sehr schön. Abschließend wird die blanke Stelle gereinigt und entfettet. Aceton funktioniert, Lackreiniger soll aber noch besser sein.
So vorbereitet kann die Stelle geschweißt werden. Die Probestelle hier war auf der Innenseite noch nicht optimal blank, das macht sich dann auch bei den Nähten sofort bemerkbar.
Um realistische Bedingungen zu schaffen wird das B-Säulen-Stück, wie in Einbaulage, an den Schweißtisch geklemmt. Woher ich meinen Tisch habe weiß ich leider heute nicht mehr, aber ein vergleichbares Exemplar habe ich unten hinzugefügt.
Dann folgten ein paar Versuche, wie die Teile bestmöglich zueinander ausgerichtet werden können. Magnete scheiden leider aus, da diese das Schweißergebnis beeinflussen. Am Ende war die beste Lösung ein seitlich von innen angeklemmter Kupferstreifen.
Die Einstellungen am Schweißgerät kann man dem Foto entnehmen. Schweißsstrom ist auf 27Es sind ein leichter Gasnachfluss und eine leichte Stromabsenkung eingestellt. Alle anderen Features sind aus. Möglicherweise könnte man da noch etwas optimieren, aber zunächst müssen eigene Fähigkeiten erworben, bzw. optimiert werden.
Ist ein bisschen wie beim Auto. Erst mal fahren lernen, die Kiste ordentlich zum Laufen bringen und dann kann man ans Feintuning gehen.
Der Luftspalt zwischen den zu schweißenden Teilen beim WIG-Blechschweißen kann, und sollte gering wie möglich sei. Die erfordert zwar im Vergleich zum Schutzgasschweißen mehr (und gründlichere) Vorarbeit, aber das Ergebnis erfordert auch weniger Nacharbeit als beim Schutzgasschweißen.
Beim Schweißen des Profils sind die Kanten das wichtigste. Diese müssen später gerade sein, da auch ungeübte sofort erkennen auf eine Linie gerade ist, oder eben nicht. Die ersten Heftpunkte kommen also an die Kanten. Also Schweißstabmaterial anschmelzen und antragen. Dann ein paar weitere auf die Zwischenräume vorne und dann die Seiten. Am Ende der Naht wird dann Kupfer untergelegt, damit die Naht dort nicht durchbrennt.
Wenn alles passt, wird nun die Schweißnaht gezogen. Die aufgesetzten Schweißperlen werden aufgeschmolzen und werden Teil der Schweißnaht. Wenn zu wenig Material vorhanden ist, oder die Naht droht durchzubrennen, kann weiteres Material hinzugefügt werden.
Ich brauche zwar noch keine Brille, aber beim WIG-Schweißen habe ich immer das Gefühl zu wenig zu sehen, wenn man genau darüber nachdenkt ist dies auch kein Wunder.
Der Schweißbereich, um den es geht, ist wirklich klein und bei entsprechender Entfernung nicht mehr optimal zu sehen. Der Schweißschirm, den ich nutze, hat eine Aufnahme für Vergrößerungsgläser. Fehlen nur die passenden Gläser. Meine pragmatische und günstige Lösung ist eine Lupenbrille mit vier Einsätzen von 1,5 bis 3,5-Facher Vergrößerung.
Die Gläser sind tatsächlich aus Glas und nicht etwa auch Kunststoff. Die 3,5-Fache Vergrößerung findet nun Platz im Schweißhelm. Die Brille mit den anderen Gläsern kann für Fummelkram genutzt werden. So kam diese mit 2,5er Lupe schon zum Geradebiegen der Beine an einem Elektronikstecker zum Einsatz.
Dank der Vergrößerung hat man die Schweißstelle und das Schmelzbad wesentlich besser im Blick. Man erkennt jedes Detail und kann besser erkennen, wie das Schweißbad reagiert. Das Schweißergebnis lässt sich besser steuern und wird somit deutlich besser.
Trotz der ungewohnten Schweißposition und -richtung ist das Ergebnis gut. Die Schweißnaht ist durchgeschweißt und das Blech ist immer noch in der Flucht.
Trotz Gasnachlauf kann es mal zu Lunkern kommen, insbesondere wenn die Bleche nicht 100-Prozentig sauber sind. In diesem Fall einfach die Schweißpistole ein kleines Stück wieder in die bereits geschweißte Naht zurückbewegen.
Die Naht würde jetzt noch bearbeitet werden, das spare ich mir aber an diesem Übungsstück.
Die WIG-Kontakte werden wieder mit der selbstgebauten WIG-Elektroden Schleifvorrichtung angespitzt.
Und weil noch etwas Zeit war, habe ich noch einen Teil des alten Unterschrankes der Werkbank, die mal aus Küchenschränken bestand, mit der Japansäge gekürzt, sodass der dahinter befindliche Raum besser zugänglich wurde. Nun ist dort ca. 1 m2 Lagerfläche für selten genutztes Material.