Hier zeige ich euch mal den Elektroantrieb / Motorantrieb meiner Sickenmaschine. Diese Ausführung kann mit Anpassungen auch für andere Sickenmaschinen oder andere langsam drehenden Geräte/Dinge genutzt werden.
Dies hier ist keine Anleitung oder Aufforderung das Gezeigte nachzubauen. Es zeigt lediglich einen privat genutzten Aufbau. Es wird keine Garantie oder Haftung für Nachbauten oder dadurch entstehende Folgen übernommen.
Aber nun zur Sickenmaschine:
Der Weg zu dieser Sickenmaschine war relativ lang.
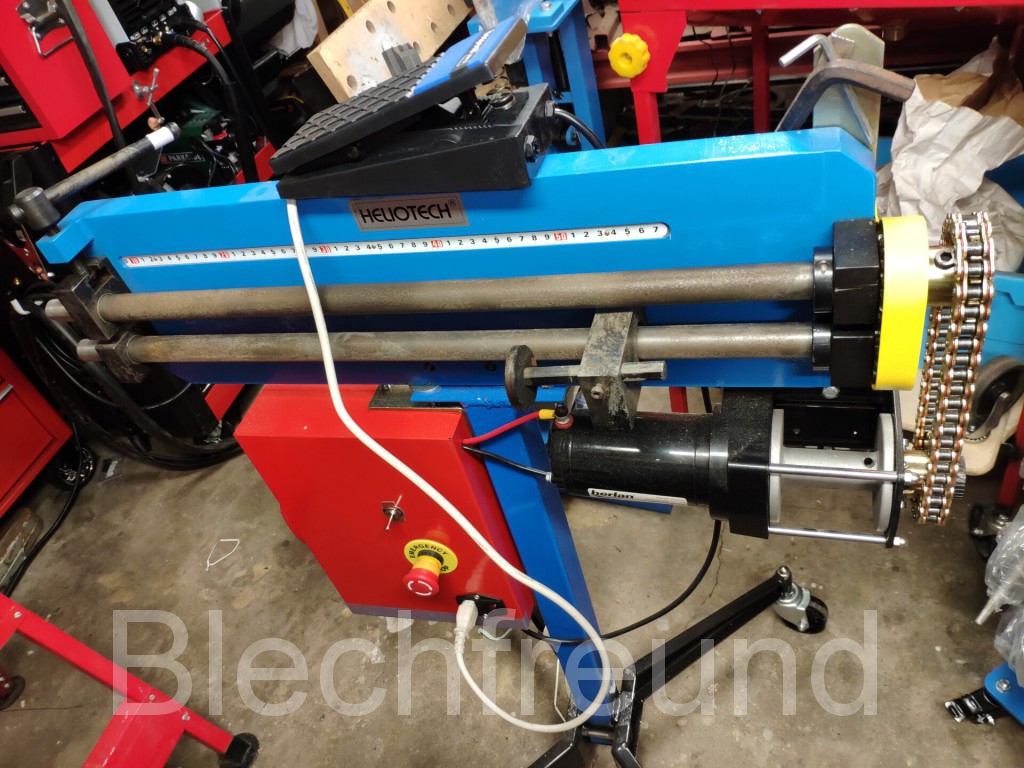
Wenn man sich mit Blechumformung beschäftigt, kommt man früher oder später zum Thema Sickenmaschine.
Neben den Sicken kann man unter anderem auch Bleche abkanten und dies nicht nur an gerade Stecken, sondern auch an Rundungen. Der Traum war also eine solide, nach Möglichkeit elektrisch angetriebene Sickenmaschine.
Aber diese waren noch Profiwerkzeug und entsprechend teuer.
Der erste Versuch war somit, eine gebrauchte uralte Sickenmaschine, mit 4 Rollen. Ein unglaublich robustes und schönes Werkzeug, aber leider nicht für meine Zwecke geeignet. Es gab keine passenden Rollen und die Einlegetiefe war für größere Bleche ungenügend.
Für erste Experimente war sie aber gut. Es war dann klar, es muss etwas Besseres her.
Das Gerät wurde zwei Jahre, nachdem eine neue Sickenmaschine Einzug gehalten hat, schweren Herzens mit leichtem Gewinn weiterveräußert.
Die neue Sickenmaschine kam im September 2015, nach endlosen Recherchen und Preisvergleichen und einem netten E-Mail-Kontakt direkt mit dem Hersteller Heliotech aus Polen. Entgegen den günstigen optisch ähnlichen Sickenmaschinen aus China ist dieses Exemplar zwar teurer, aber außerordentlich solide. Der Körper ist ein CNC-Brennteil aus einer 30 mm Stahlplatte. Trotz der üppigen Einlegetiefe von 550 mm ist der Körper stabil und verwindungssteif. Die massive Ausführung macht sich auch im Gewicht bemerkbar. Das Teil wegzulegen, wenn es nicht genutzt wird und bei Bedarf im Schraubstock einzuspannen, war die Ursprungsidee, wurde aber schnell durch einen behelfsmäßigen Standfuß ersetzt.
Auch dies war nur eine Notlösung, bei der es sich um einen bereits einfachen Motorhalter handelte. Zwar nicht optimal, aber für die Anfertigung des BMW E36 Bodenblechs hat es funktioniert. Dazu aber später mehr, wenn der Bericht dazu online geht.
Bei der Anfertigung des Bodenbleches tauchte auch ein weiterer Kritikpunkt auf. Die Kurbel der Sickenmaschine ist ebenfalls aus Stahl und extrem schwer. In der Aufwärtsbewegung macht sich dies negativ bemerkbar. Besonders, wenn man mit zwei Händen das Blech führt und mit der fehlenden dritten Hand die Kurbel betätigen muss.
Da ich mal an einer elektrischen Sickenmaschine arbeiten durfte, war klar, dass auch diese einen elektrischen Antrieb bekommen sollte. Am einfachsten wäre natürlich eine Fertiglösung gewesen, aber diese gab es nicht, und was es gab hätte noch angepasst werden müssen und war preislich völlig außerhalb des Hobby-Rahmens.
Vielleicht kann man ja selber die Sickenmaschine aufrüsten.
Umbau der Sickenmaschine auf elektrischen Antrieb
Nach einigem Recherchieren und Überlegen wurde im Februar 2020 der Umbau gestartet.
Die Elektrik war also einsatzbereit, nun ging es darum das ganze mit der Sickenmaschine zu kombinieren.
Die waagerechte untere Strebe des Motorständers war das optimale Halbzeug für den Ständer der Sickenmaschine. Die Füße und Rollen kamen von einem billigen Getriebeheber. Ähnliche Modelle sind ganz unten abgebildet. Dort finden sich auch die weiteren von mir genutzten Komponenten und die entsprechenden Produktbeschreibungen.
Als Antriebsmotor wurde eine PKW-Seilwinde (ohne Seil) vom Hersteller Berlan verbaut. Der Motor ist mit einem Stahlhalter (Torbeschlag) an die Sickenmaschine angeschraubt.
Die Kraftübertragung durch Ritzel und Kette aus dem Motorradzubehör.
Die Steuerung der Seilwinde wurde nicht genutzt, da diese keine Geschwindigkeitsregelung hat. Stattdessen kommt ein regelbares Netzteil zum Einsatz, dieses liefert aus 230 Volt Netzspannung eine einstellbare Spannung von 0 bis 24 Volt. Eine Digitalanzeige zeigt den gewählten Wert an.
Ich habe ein Exemplar aus China bestellt, jedoch ist dies auch bei Amazon erhältlich. Hier findet ihr auch eine genaue Produktbeschreibung und eine Bestellmöglichkeit.
Mit dem Netzteil ist nun eine stabile Stromversorgung gewährleistet. Da der Motor jedoch vorwärts und rückwärts drehen soll und das ganze dazu auch noch in einer regelbaren Geschwindigkeit wird ein weites Bauteil benötigt.
Auch dieses wurde zunächst in China bestellt. Aber auch dies gibt es bei Amazon. Es handelt sich dabei um einen Motor Drehzahlregler mit Digitalanzeige (nicht wirklich nötig aber praktisch) und einem Richtungsumschalter.
DC Motor Drehzahlregler, DC10V-55V PWM Reversible Motor Controller Schalter mit Digitalanzeige – Bei Amazon
Am Motor Drehzahlregler findet sich ein Potentiometer zur Einstellung der Motorgeschwindigkeit und Schalter zum Wechsel der Drehrichtung.
Da die Sickenmaschine möglichst mit dem Fuß gesteuert werden soll, um die Hände zur Führung der Bleche freizuhaben, waren einige weitere Überlegungen erfolderlich.
Am schönsten wäre ein Pedal gewesen, dass wie eine Wippe funktioniert und alle Funktionen kombiniert. So etwas gibt es jedoch scheinbar nicht.
Industriepedale aus Metall haben meist nur die Funktion “ein” oder “aus”. Damit wäre eine Kombination aus zwei Pedalen möglich. Die Drehzahl wäre fest einzustellen über einen Drehregler. Ein Pedal wäre für Vorwärts eins für Rückwärts. Diese Lösung würde Platz kosten und scheint wenig sinnvoll, da man zum Regulieren der Geschwindigkeit doch eine Hand braucht.
Die gewählte Lösung für die ich mich entschieden habe ist ein Musikpedal für die Regelung der Lautstärke von Gitarren. Diese hat ein Potentiometer verbaut und der Motor kann somit von aus bis zur benötigten Drehzahl geregelt werden. Das folgende Pedal kam bei mir zur Anwendung.
Bespeco VM12 Gitarre Volumen Mono Pedal – Bei Amazon
Die Umkehr der Drehrichtung erfolgt an einem stabilen Schalter. Dieser ist auch locker mit dem Knie bedienbar, wenn die Hände gebraucht werden.
Aerzetix – Unterbrecher, Schalter Switch Kippschalter SP3T ON-OFF-ON 10A/250V 3 Positionen – Bei Amazon
Da es sich hier um eine kraftvolle Maschine handelt, von der auch ein gewisses Verletzungsrisiko ausgeht, wurde zur Sicherheit ein Not-Aus-Drucktaster verbaut, der das System schnell Stromlos schalten kann.
Taiss / 22mm 2 NC Roter Pilz-Verriegelungs-Not-Aus-Druckschalter 10A 440V (Garantie 3 Jahre) LA38A-02ZS -Bei Amazon
Die Stromversorgung erfolgt über ein Kaltgeräte-Netzkabel. Dazu wurde eine Buchse mit beleuchtetem Schalter und Sicherung verbaut.
Verbaut wurde die komplette Steuerung nicht in einem einfachen Schaltkasten, sondern in einem Werkzeugkoffer von Bauhaus. Dieser ist günstig, stabil für die Aufnahme der o.g. Komponenten und sicher zu verschließen.
Hilfreich für die Verkabelung waren auch die folgenden Verbinder.
Die Motorritzel habe die Bezeichnung “Motorritzel 428 Honda GX Ritzel für Motor, Kart Kette DM22 Welle, 16 Zähne”. Diese sind bei verschiedenen Anbietern verfügbar, zum Teil mit deutlichen Preisunterschieden.
Dazu braucht man dann noch eine passende Kette und ein Werkzeug, um die Kette anzupassen.
Die Kette bekommt noch eine Abdeckung.
Diese Selbstbaulösung kostet nur den Bruchteil einer Fertiglösung und bietet dabei noch den Mehrwert eines Notaustasters und im Gegensatz zu den allgemeinen Lösungen, bei denen der Motor als Verlängerung der Achse angeflanscht wird, ist hier der Motor platzsparend und kippsicher platziert.
Unten findet ihr noch ein Link zu einem Video zur Demonstration der Funktionsweise.